Engineered wood products have become integral in constructing various items, ranging from furniture to flooring. Among these, Medium Density Fiberboard (MDF) stands out as a versatile and widely-used material. This comprehensive guide explores what MDF is, its composition, the manufacturing process, and its diverse applications.
What is MDF?
Medium Density Fiberboard, or MDF, is a type of engineered wood product. It is a dense and flat panel manufactured by bonding organic wooden fibers with resin and wax, utilizing high temperature and pressure in the process. MDF serves as a crucial building material for residential and commercial properties, finding applications in furniture, flooring, and more.
Composition of MDF Boards
1. Wooden Fiber:
The primary component of MDF is wooden fiber. These fibers can be sourced from various wood species or derived from wood residues and agricultural wastes like sawdust or wood shavings.
2. Adhesive:
The adhesive used to bond the wooden fibers is typically a synthetic resin, with Urea Formaldehyde being a commonly employed option.
3. Wax and Preservative:
- Wax: Paraffin wax is added in either melted form or dissolved in mineral spirit.
- Preservative: Included at the mixing stage of the adhesive, with options like Trichlorophenol or Sodium Pentachlorate.
Manufacturing Process
The process involves mixing wooden fibers with resin and wax. This mixture undergoes high-temperature heating and pressing to form an MDF board. Modern technology ensures uniform density and eliminates issues like knots, twists, and bonding defects. The panels are finely sanded to achieve a smooth surface, making them ideal for various finishes such as carving, painting, lacquering, and veneering.
Uses of MDF Board
- Economical Furniture: MDF boards are extensively used to construct affordable furniture like bookshelves and entertainment centers, contributing to cost-effective manufacturing.
- Transportability: Lightweight MDF boards are employed in applications requiring regular movement, such as mobile homes, tradeshow booths, and theater sets.
- Cabinets: MDF is a common choice for interior cabinets, including kitchen cabinets and shelving units. Wood laminates often provide a natural wooden appearance to MDF cabinets.
- Flexibility: Flexible MDF boards, with the ability to bend or curve, find use in creating items with significant curves or slopes.
- Fire Retardant: MDF boards with fire-retardant properties are crucial in constructing commercial buildings and homes where meeting safety standards is imperative.
- Moisture Resistance: Special resin in MDF boards provides moisture resistance, making them suitable for flooring, furniture, and items used in damp environments.
- Roofing Material: MDF serves as an excellent backing material for roofing shingles.
- External Usage: Specifically formulated MDF panels, resistant to moisture, rot, and termites, are ideal for external applications such as doors and outdoor architectural products.
- Soundproofing: MDF’s soundproofing properties make it valuable in creating speaker casings, walls in media rooms, and floor underlayment to prevent sound transmission.
- Shelf Panels: MDF panels designed for display purposes secure shelves in retail stores, often featuring deep grooves.
In conclusion, Medium Density Fiberboard, with its diverse uses and adaptability, has become a cornerstone in the world of engineered wood products. Its cost-effectiveness, coupled with unique properties like flexibility, fire resistance, and soundproofing, makes it an indispensable material in various industries. Understanding what MDF is, how it’s made, and its broad applications sheds light on its significance in modern construction and manufacturing.
Related blogs
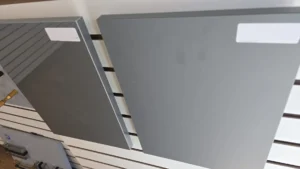
An Analysis of the Advantages and Disadvantages of Different Edge Treatment Methods for Melamine Plywood
Melamine plywood, a material widely used in furniture manufacturing, interior decoration, and other fields, has

Additives Used in Plywood Glue: Functions and Benefits
Additives are essential in plywood glue formulations, enhancing the performance, durability, and environmental friendliness of

Synchro Plywood: A High-Quality Composite for Realistic Wood Finishes
What is Synchro Plywood? Synchro Plywood is an innovative composite material designed to emulate the

The 5 Best Kitchen Cabinet Materials: Pros and Cons
Choosing the right material for your kitchen cabinets is essential for both style and durability.